Update: connecting to the extruder carriage
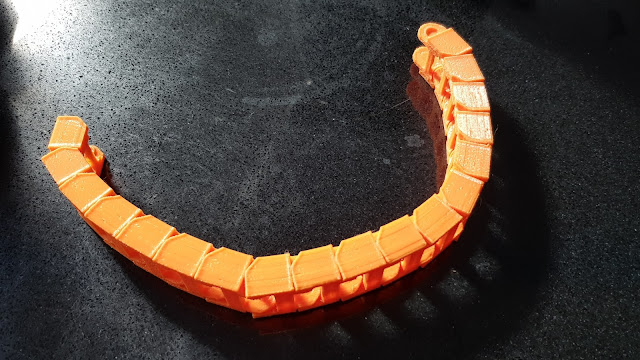
One thing which I hadn't been able to decide upon was how best to get the cabling to the X carriage for the extruder and other elements. I had toyed with a cable from the gantry and this would be been fairly simple, but it would also leave quite a lot to be desired aesthetically. The other plan was to use cable chains to traverse the X and Z movement. This is a lot more fiddly, but is likely to give a much better result. It will, however, need quite a few more parts to be designed. I decided that it would be worth a try to see how best to achieve this and I came up with a rough idea. To realise this, I needed a narrower chain than that which I'd used for the Y-axis (where the dimensions are less critical). So, I decided to simply scale the model I've used there to create a link 20mm wide. I did this and left a large number printing to create a test chain. Unfortunately the scaling has also meant that the clearances were reduced too and I ended up with a chain which was ver